Customer meeting 20.07.21
Attendees:
- Harald Buys: CIO & Lead of Competence Center; responsible for all tools and digitization efforts
- Jean-Pierre Schiertz: In Jean-Marc's team; responsible for central forecasting
- Marcel Arts: Team Lead Logistics
- Jean-Marc Albert: Responsible for strategic stock & sourcing management; project manager, e.g. for S&OP or improvement projects between sites
Requirements:
- Resources for data and IT should not be a problem but expectation is that for POC no IT data connection is needed
- 2 years of demand data is already available in Excel and can easily provided
Goals:
- "We do not plan to bring in a new application" → planning is done mostly in SAP
- Deliverables: Forecasts, Stock/Supply, aggregated across multiple sites
- Impact on improvement is assessed in different categories: A, B, C and 'New products'
Scope:
- "2020 was a crazy year - does it make sense to do a forecast exercise for that period"
- Scenario 1 - Everything: 25-27 warehouses; 300.000 product_site_ids
- Scenario 2 - Windscreens: 25-27 warehouses, 90.000 product_site_ids
- Scenario 3 - Windscreens Portugal: 2 warehouses, 3.500 SKUs (product_site_ids to be confirmed, probably 7.000 product_site_ids)
Current process:
- Forecast is creates every 2 months, aggregated on country level, 6 months horizon —> to be changed to 12 months
- Jean-Pierre is creating forecast centrally, 1 person in each country responsible for reviewing the numbers and modifying if necessary
- Performance tracking on stock management → there are currently running a stock optimization project on one of the sites
- Monthly pulling of 'Product availability'
- Top 300 Out-of-stock products
- Forecast Accuracy is tracked via Dashboard, on aggregated country level per month
- Green = >90%, Yellow = >80%, Red = >70%
- Baseline: On aggregated global level = 93%-95%, on country level very different (e.g. Germany between 95%-99% but Portugal much less)
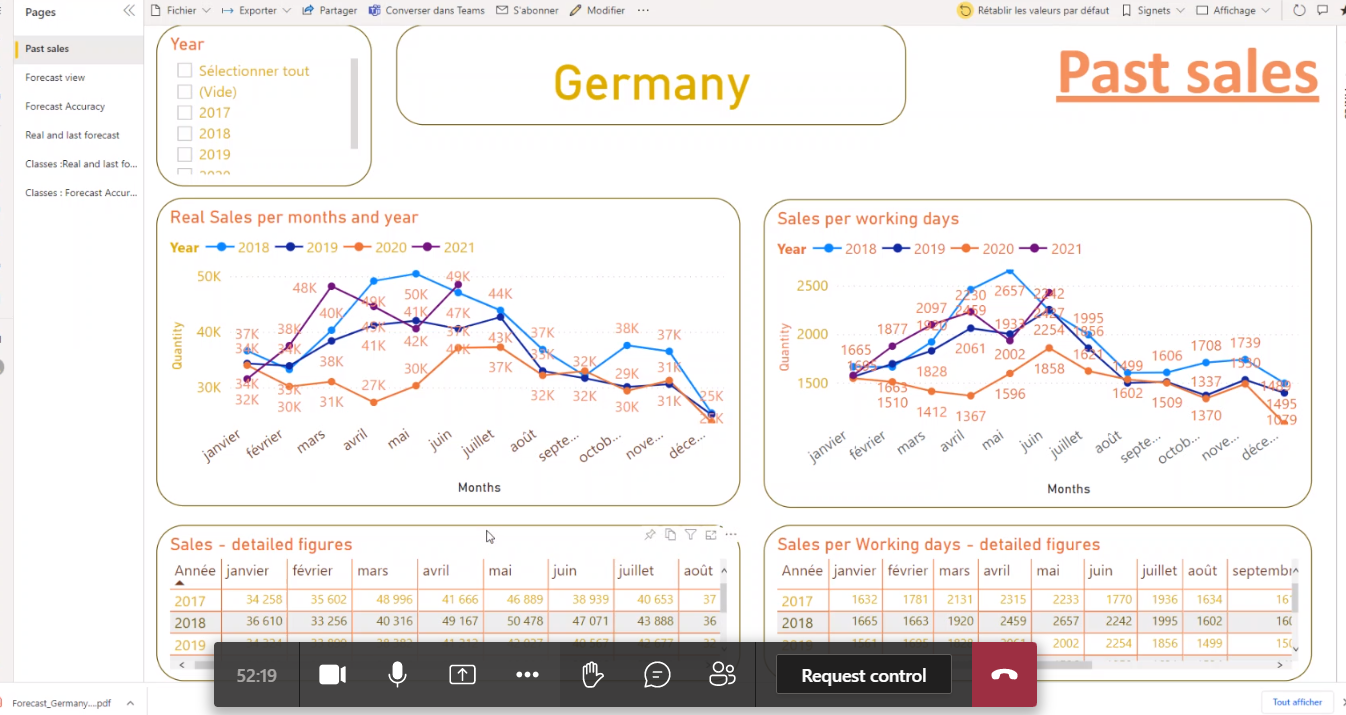
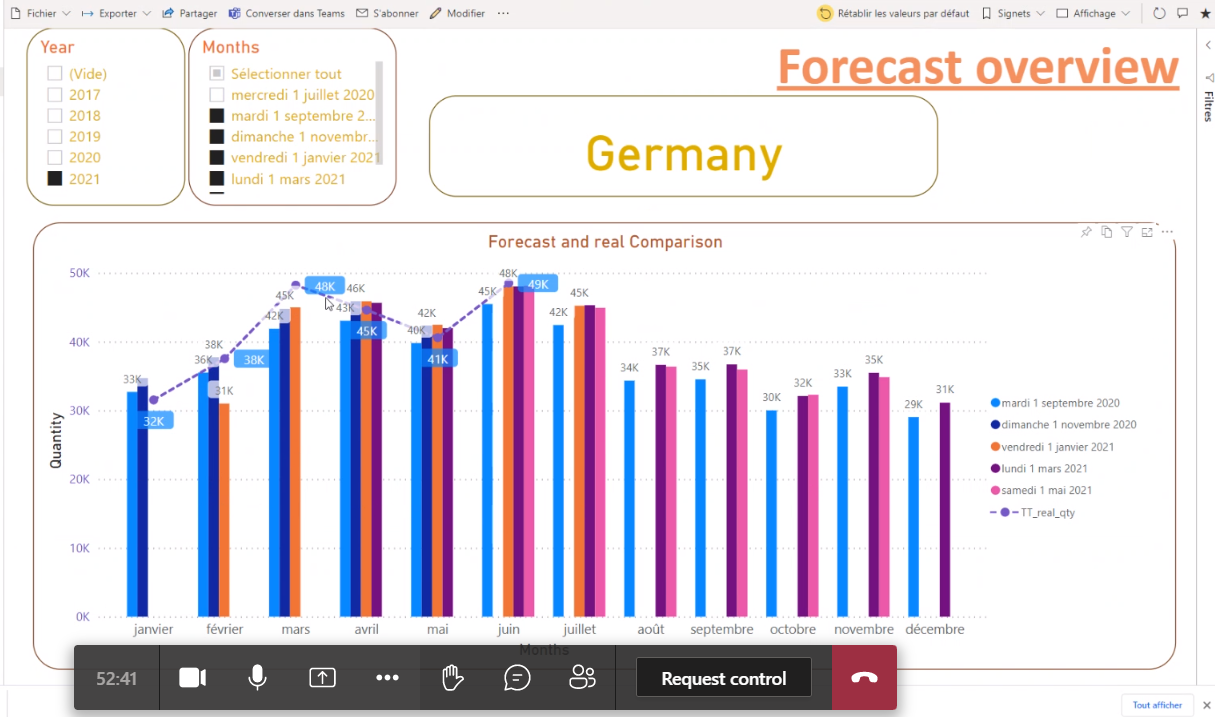
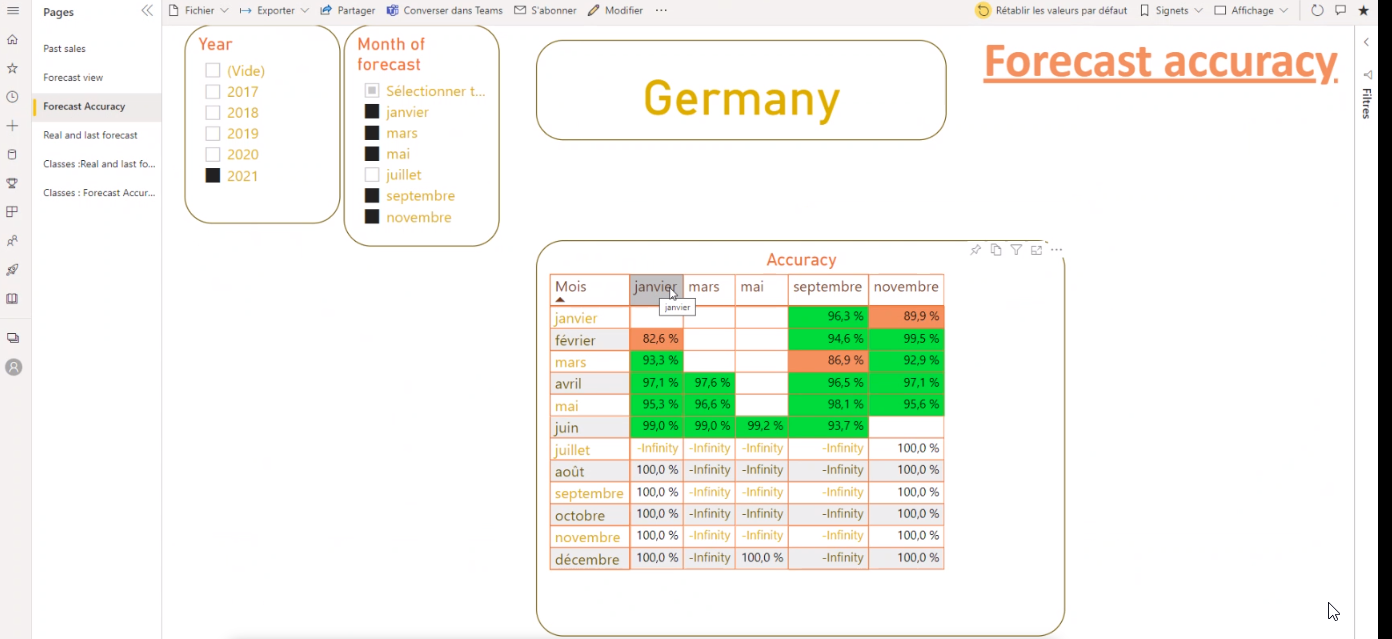
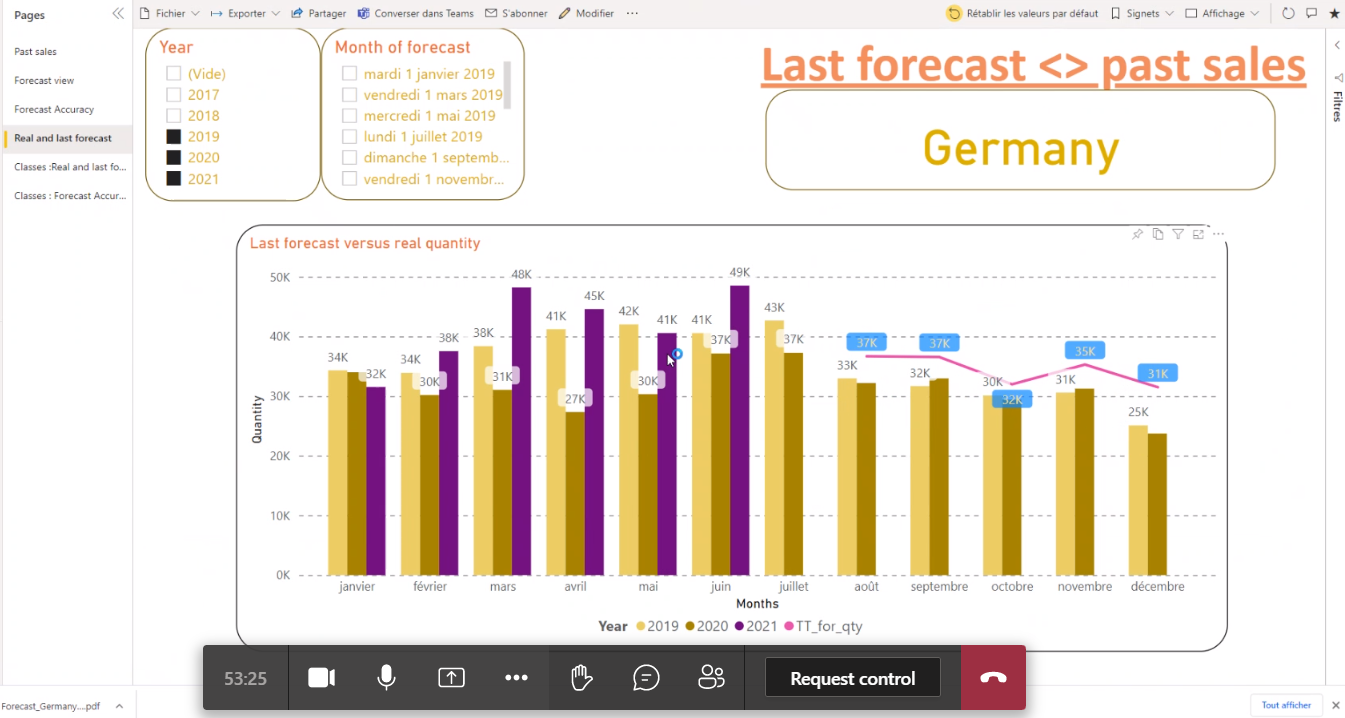
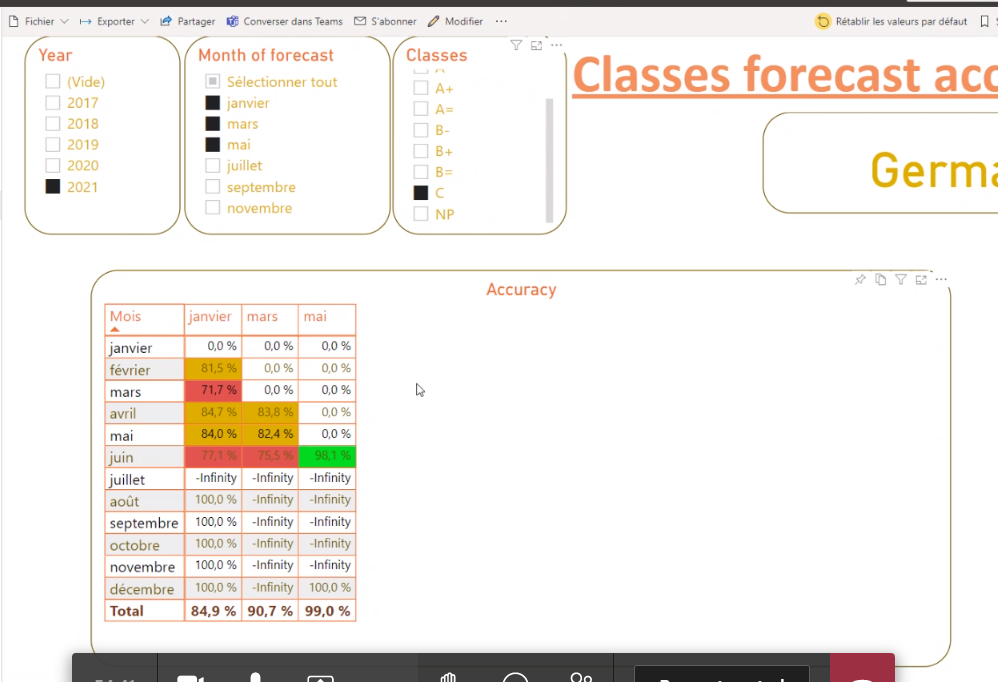
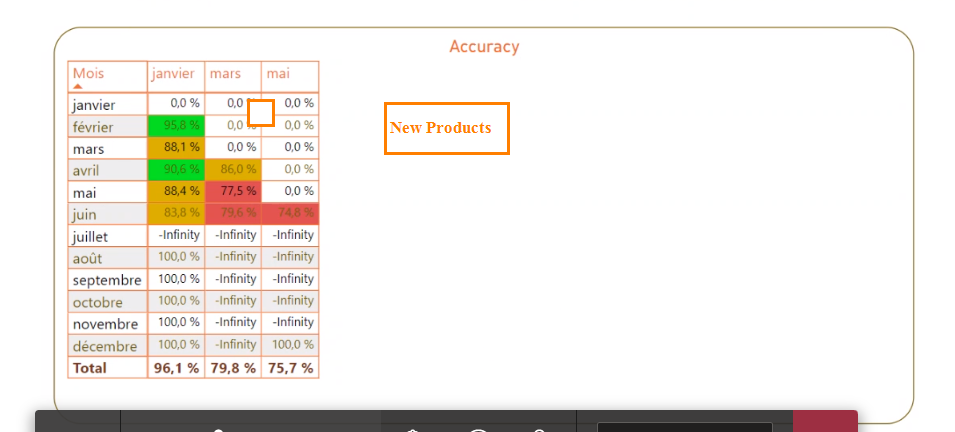